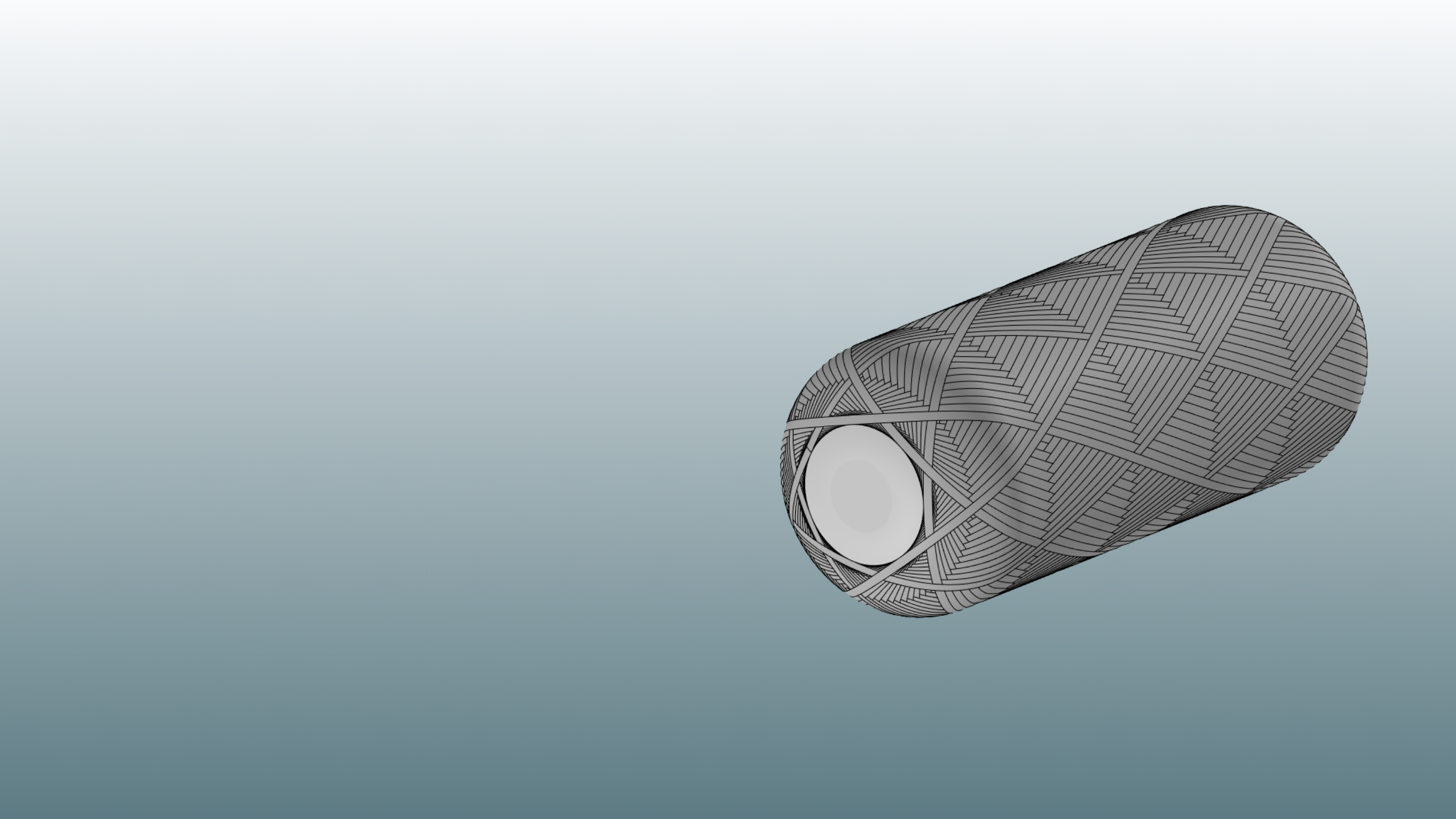
Composite Engineering
Benefit from our expertise to optimize your composite products
TANIQ has 18 years of experience assisting clients with developing new products and production processes. The core of our expertise lies in the design and robotic winding and placement of composite products. Our experience with product development and in-house design and prototyping capabilities help our clients to develop their products in a shorter period and at a lower cost.
For developing new products and processes we offer Feasibility Studies wherein we collaborate closely with our clients to determine the technical and/or financial feasibility. Typical activities are product design, prototype development and testing, process development, and return-on-investment calculations. As an R&D company we are experienced and efficient in developing innovative solutions. Our in-house developed TaniqWind software enables us to make custom software solutions for our clients. We have an in-house prototyping facility with two robotic winding systems, curing oven and a 400-ton press.
TANIQ is a valuable development partner, offering:
18 years of R&D experience
Expertise in robotic filament winding
Powerful design and manufacturing tools
Robotic winding systems for R&D and prototyping
Taniqwind software platform
Below you can find more information on our composite development capabilities:
Filament Winding Expertise
TANIQ started developing composite products based on filament winding in 2006. Since then, TANIQ has developed many filament wound products, ranging from small tubes for the automotive industry to large 12-meter-long marine hoses. TANIQ uses their expertise and experience to assist their clients with developing their composite products and automated production processes.
Feasibility Study
For developing new composite products or production processes we propose a Feasibility Study, during which we closely collaborate with our clients to determine the technical and/or financial feasibility of the project.
The Feasibility Study follows an agile approach wherein we determine the objectives beforehand and develop a solution, based on the results and forthcoming insights obtained during the project. This approach has proven very efficient for R&D projects and has been successfully executed in our internal R&D and client projects.
TANIQ spends 50% of its time on developing composite products and production processes. TANIQ has an in-house prototyping facility with two robotic winding systems for internal and client R&D projects. In addition, there are curing ovens and an industrial 400-ton press for molding and curing.
TANIQ has experience with developing new products, and the associated mandrels, moulds and tooling design. The in-house prototyping facilities and R&D experience allow us to assist our clients in efficiently developing and testing new composite products, ensuring faster time-to-market and reduced development costs
Prototyping Facility
TANIQ has a team of software and composite engineers working on design and analysis of composite products. For designing they use TaniqWind software. This in-house developed software platform enables our experts to easily create custom solutions. For analysis, the composite designs can be converted into FE models using the FEA Toolbox, supporting shell elements, 2DA elements and 3D elements for Hyperworks and Abaqus.
Design & Analysis
Applications
TANIQ has developed a wide range of applications for demanding industries worldwide ranging from series-manufactured parts (500.000/yr) to one-off specialties. Sizes range from small DN 25mm pipes, to large DN 1.2m composite hoses up to 12m long.
An important application group are composite pressure vessels for Hydrogen storage. TANIQ has developed Type III and Type IV COPVS using wet winding, dry winding, thermoset prepregs and thermoplastic tapes. Additionally, TANIQ is part of a Dutch consortium working on the development of a composite pressure vessel for storing liquid hydrogen under cryogenic conditions.
For all these applications TANIQ is a valuable development partner, offering 18 years R&D experience, powerful design and manufacturing tools, including the robotic winding systems and TaniqWind software platform.
