
Winding Robot Configuration
Design the optimal machine configuration for your winding robot
To determine the optimal machine configuration we typically start with the product dimensions and winding process (e.g. thermoset towpreg). From there, we design the type of robot arm needed and its relative position to the spindle. If needed, the robot can be placed on a track to increase its reachability. Another important aspect is the guiding of the materials to the winding tool. Depending on the material type and number of fibers/tapes, a tensioner system is designed. For large products, the robot can be positioned on a track, and a large number of creels move on the track alongside the robot.
In another type of configuration, the robot holds and rotates the mandrel, while guiding the product by a winding tool on a fixed position. The advantage of this configuration is the minimum feed through length and guiding of the material. This solution is limited in product size since the robot needs to hold and manipulate the mandrel.
Overview of common filament winding robot configurations
The Scorpo systems can be adapted as is, or customised to requirements. To provide an overview of the system:
The standardised Scorpo Robotics can be used as a foundation for a customised setup. Examples of customisation:
Robotic arm (model and position)
Robotic arm pedestal or track
Special tensioner (number of positions)
Custom robotic tools
Custom tool station (number of tools/positions)
Mandrel rotator (axis-length, hight, position and power)
General layout of robot cell
Touchscreen interface
Safety system
Doors and fence
In addition, completely custom cells can be developed.
Scorpo Leo
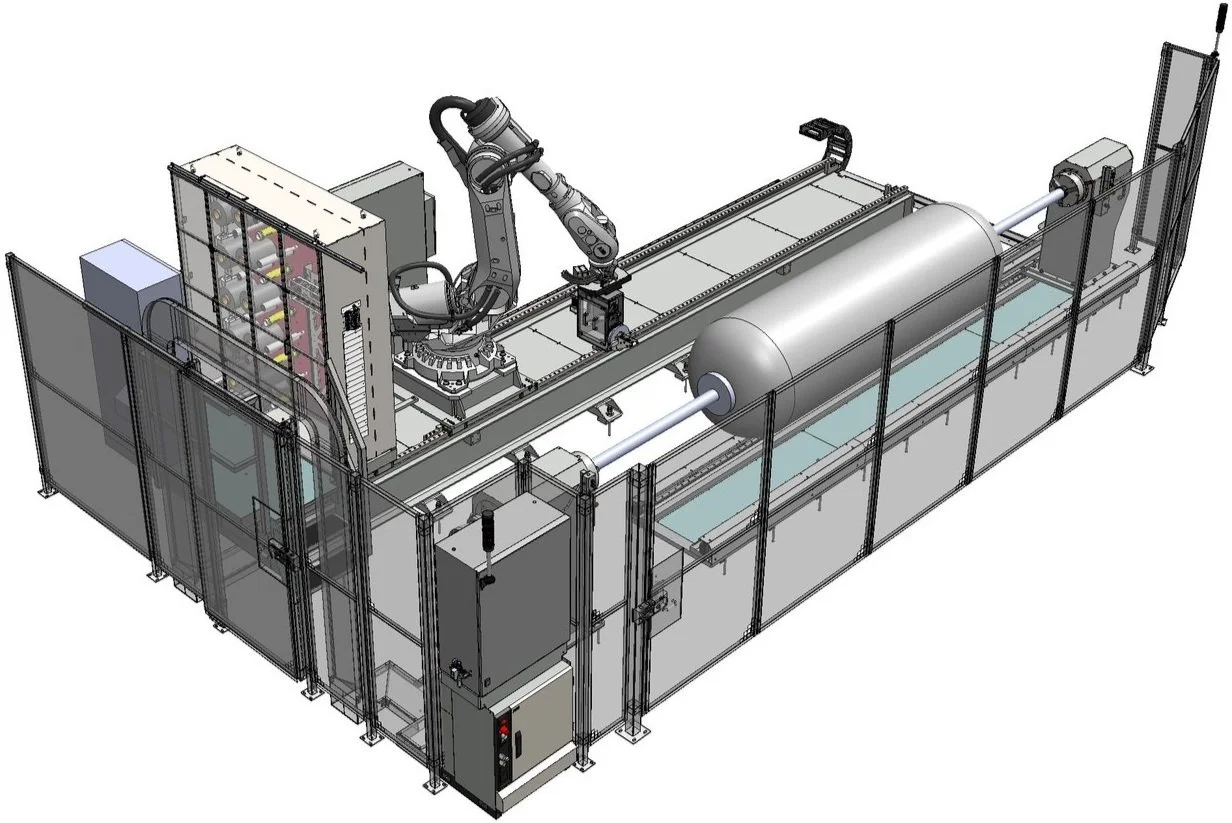
Rendering Overview
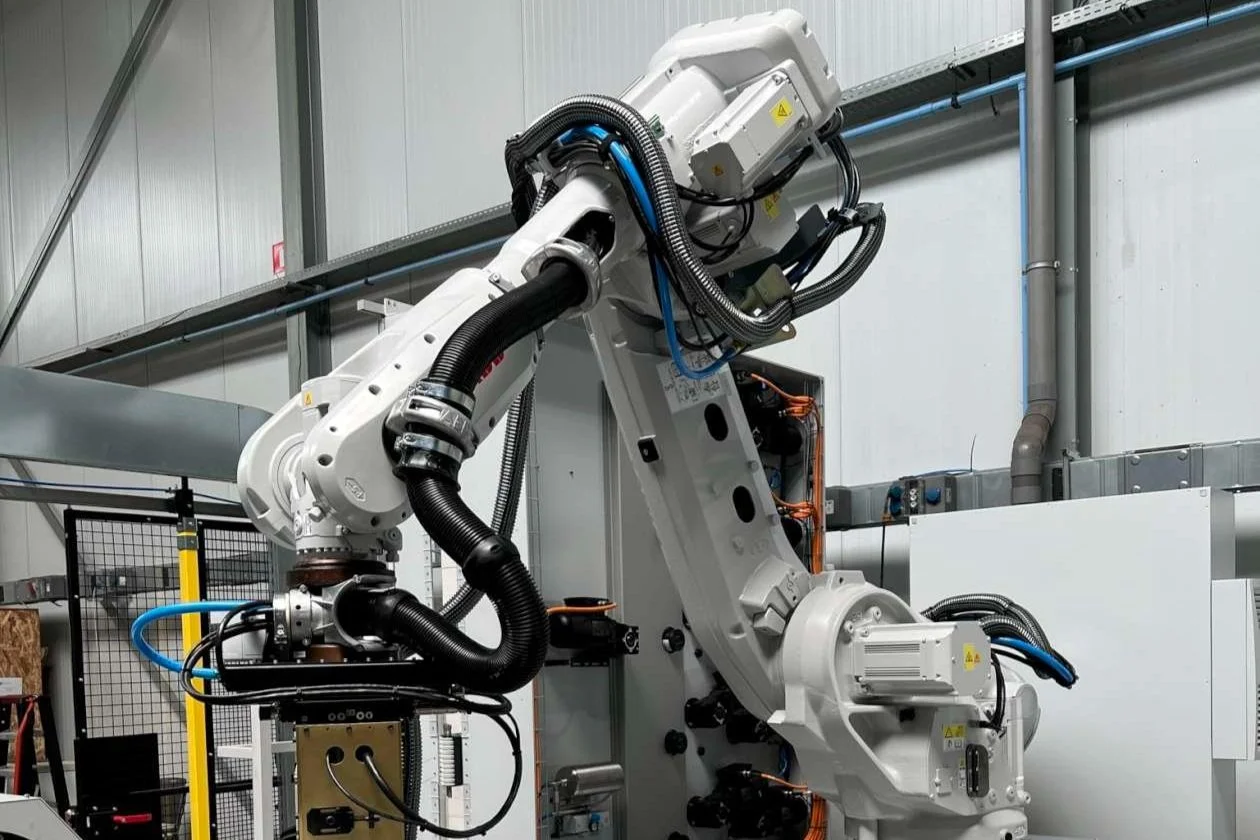
Robot Arm
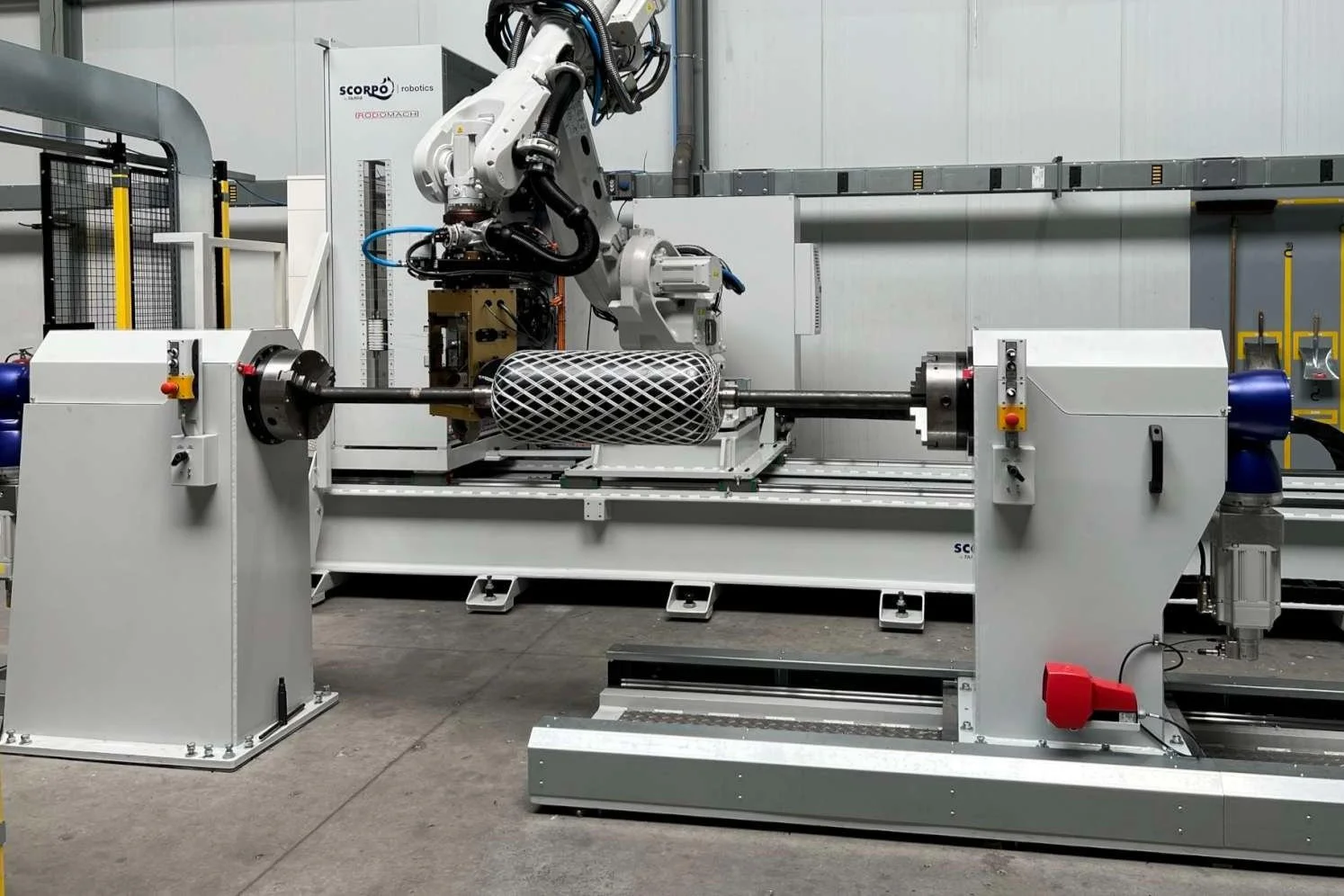
External Axis/Mandrel
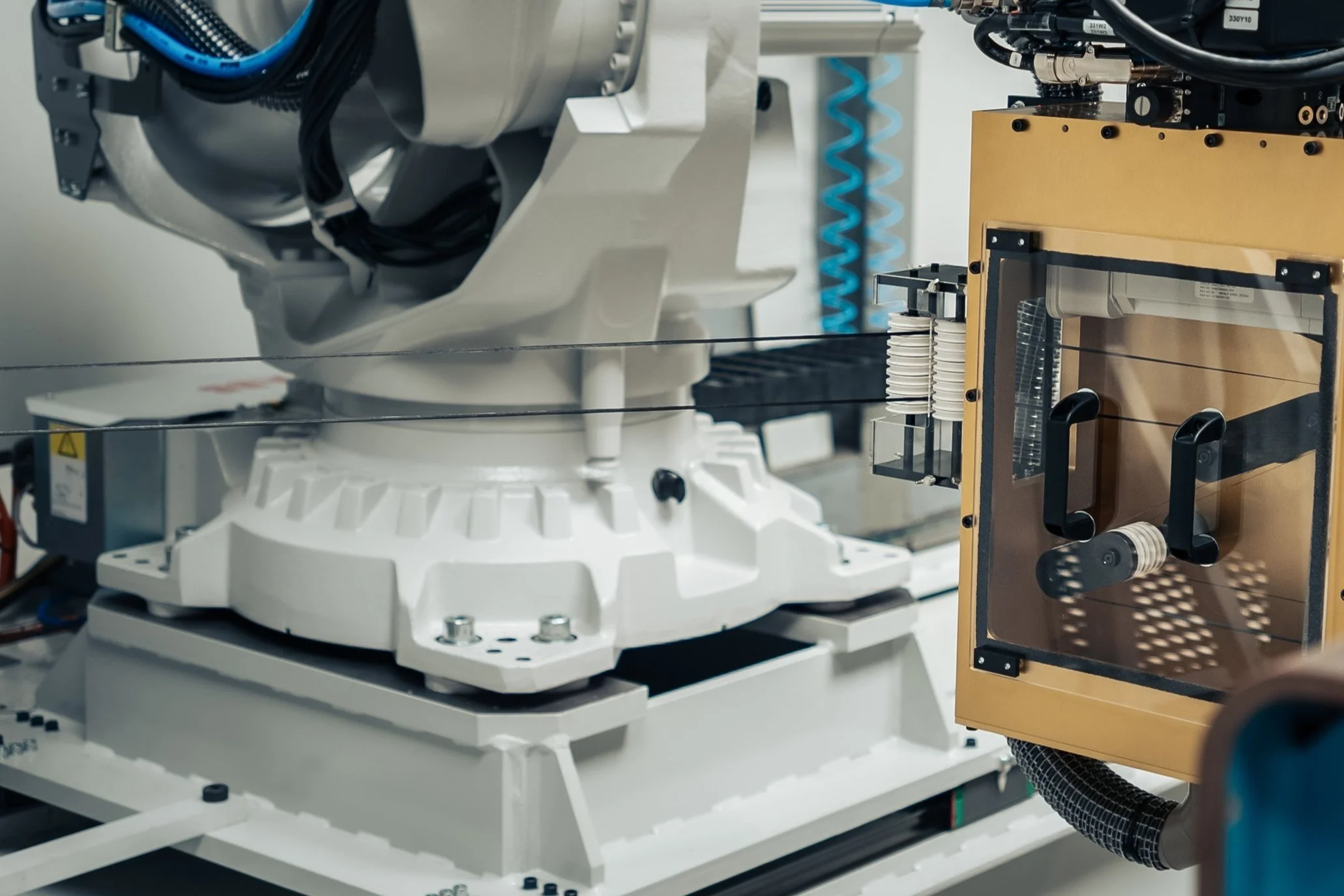
Pedestal/Track
Scorpo Virgo XL
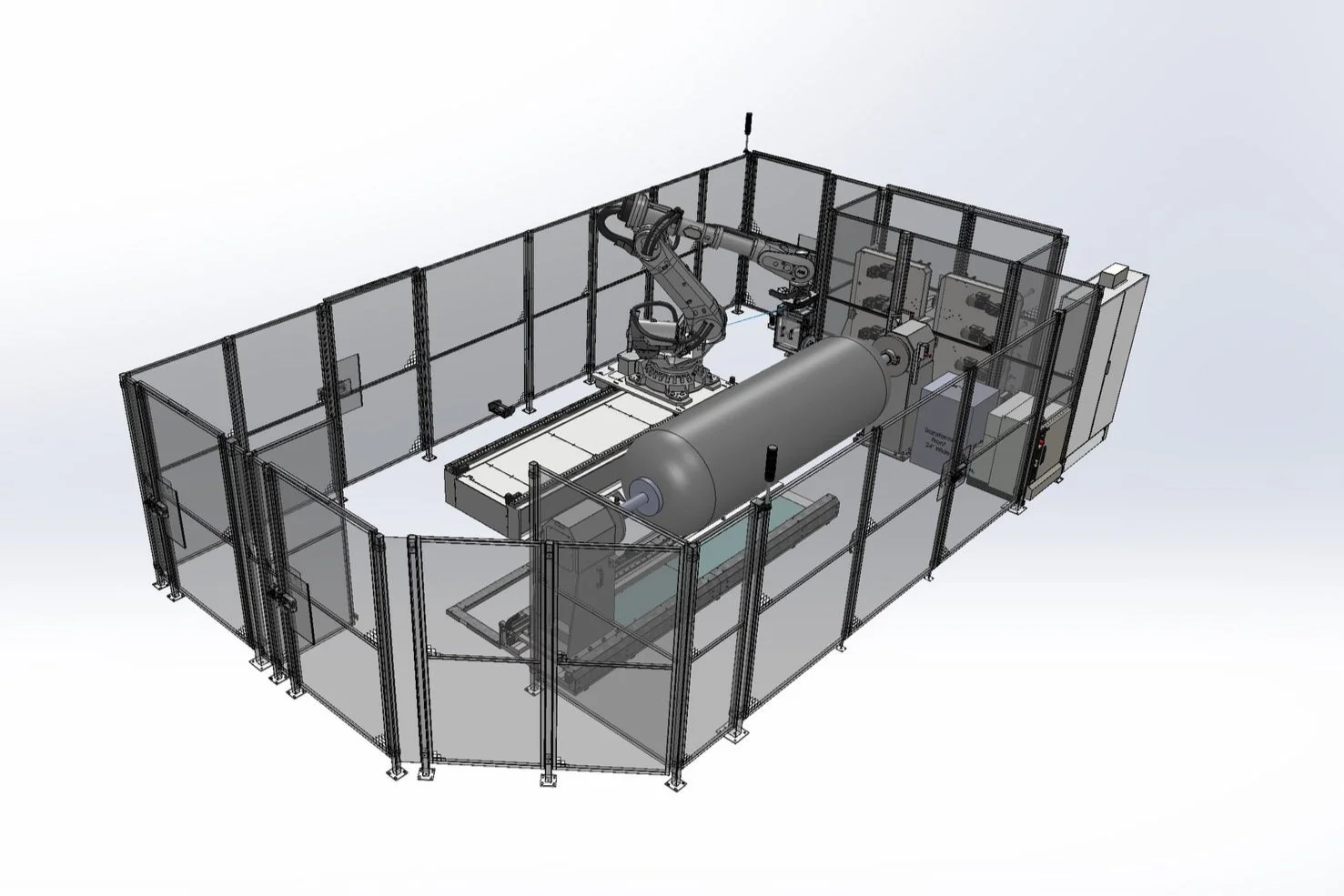
Rendering Overview
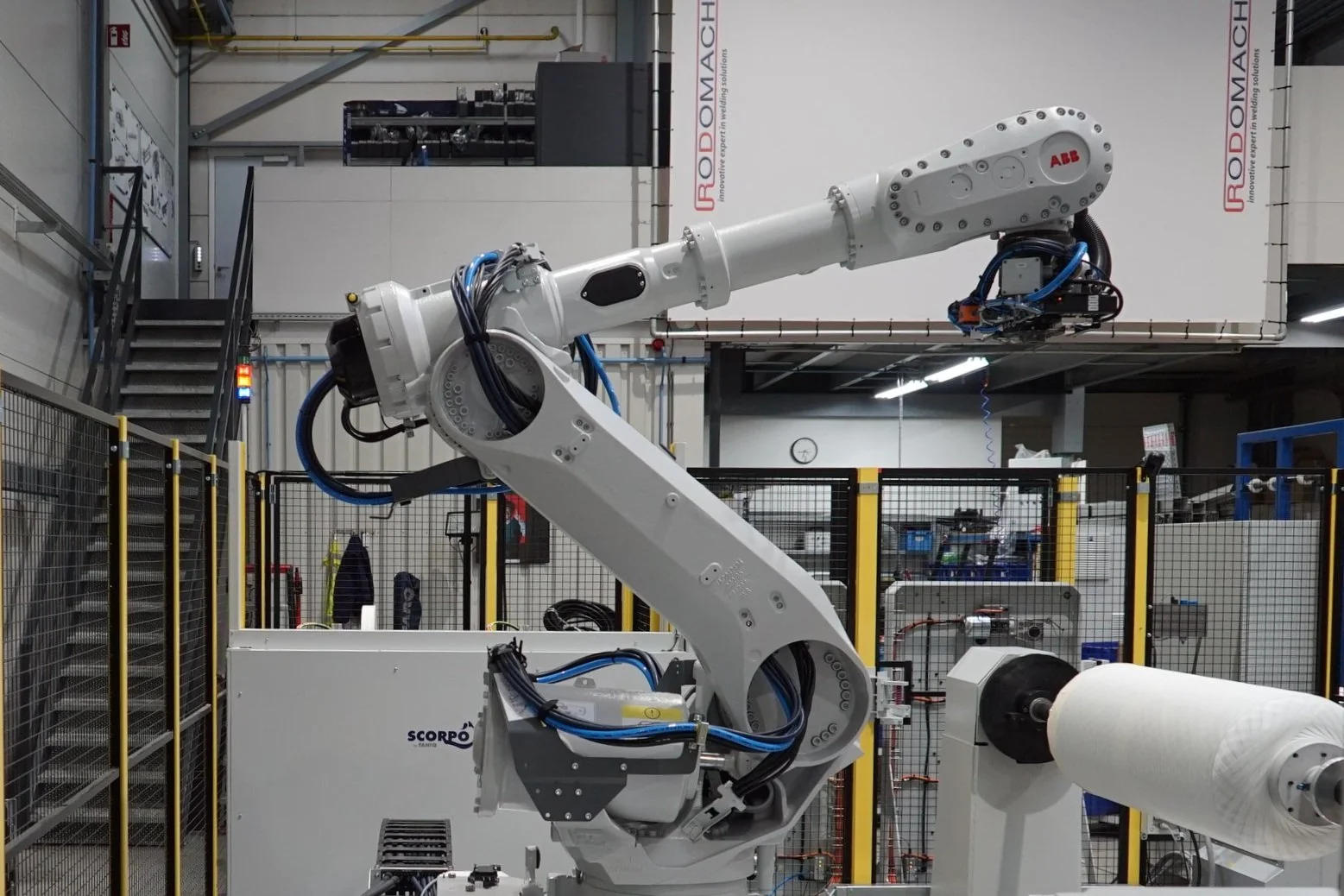
Robot Arm
External Axis/Mandrel
Pedestal/Track
Scorpo Virgo
Rendering Overview
Robot Arm
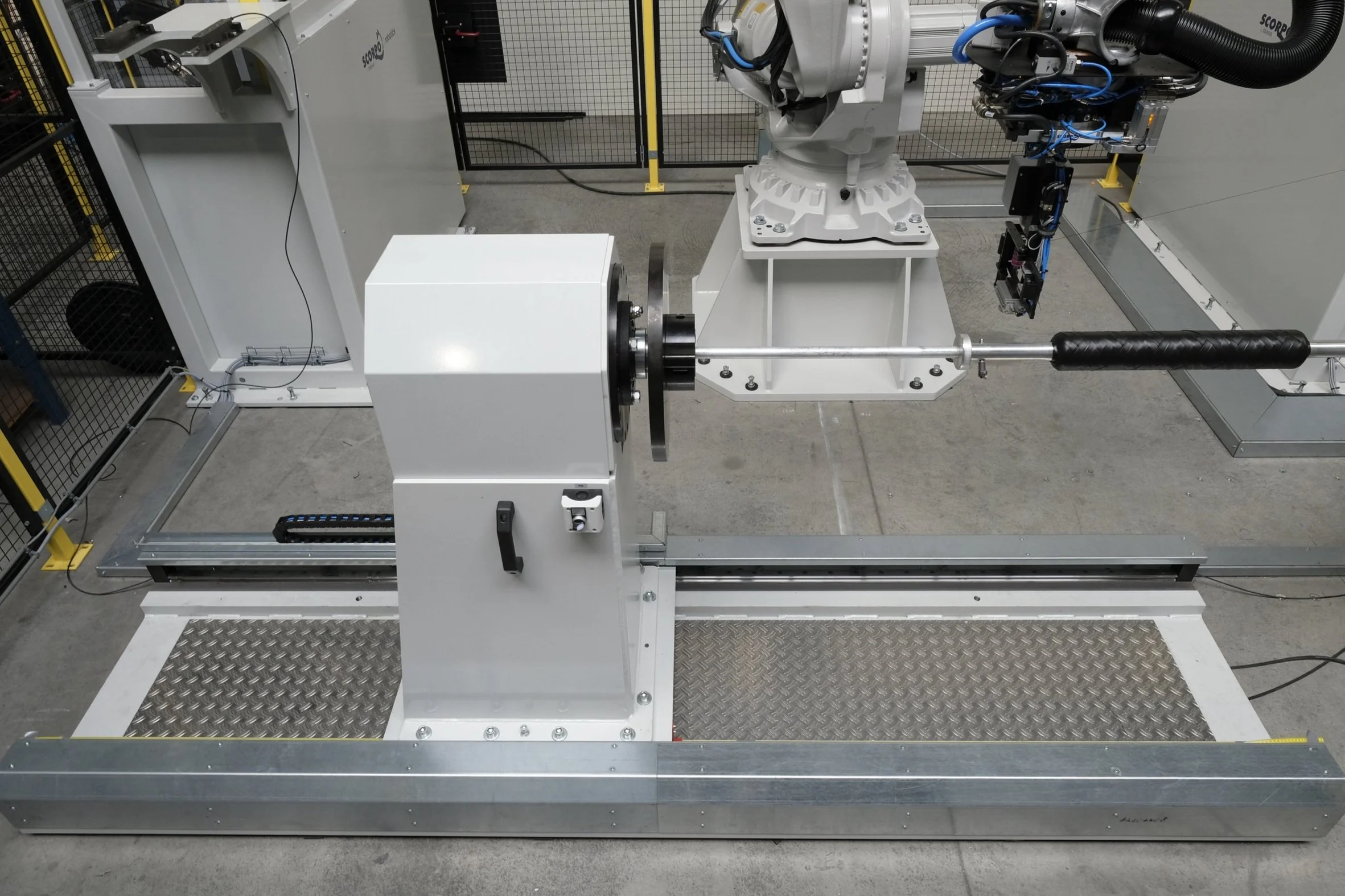
External Axis/Mandrel

Pedestal
Scorpo Taurus

Rendering Overview
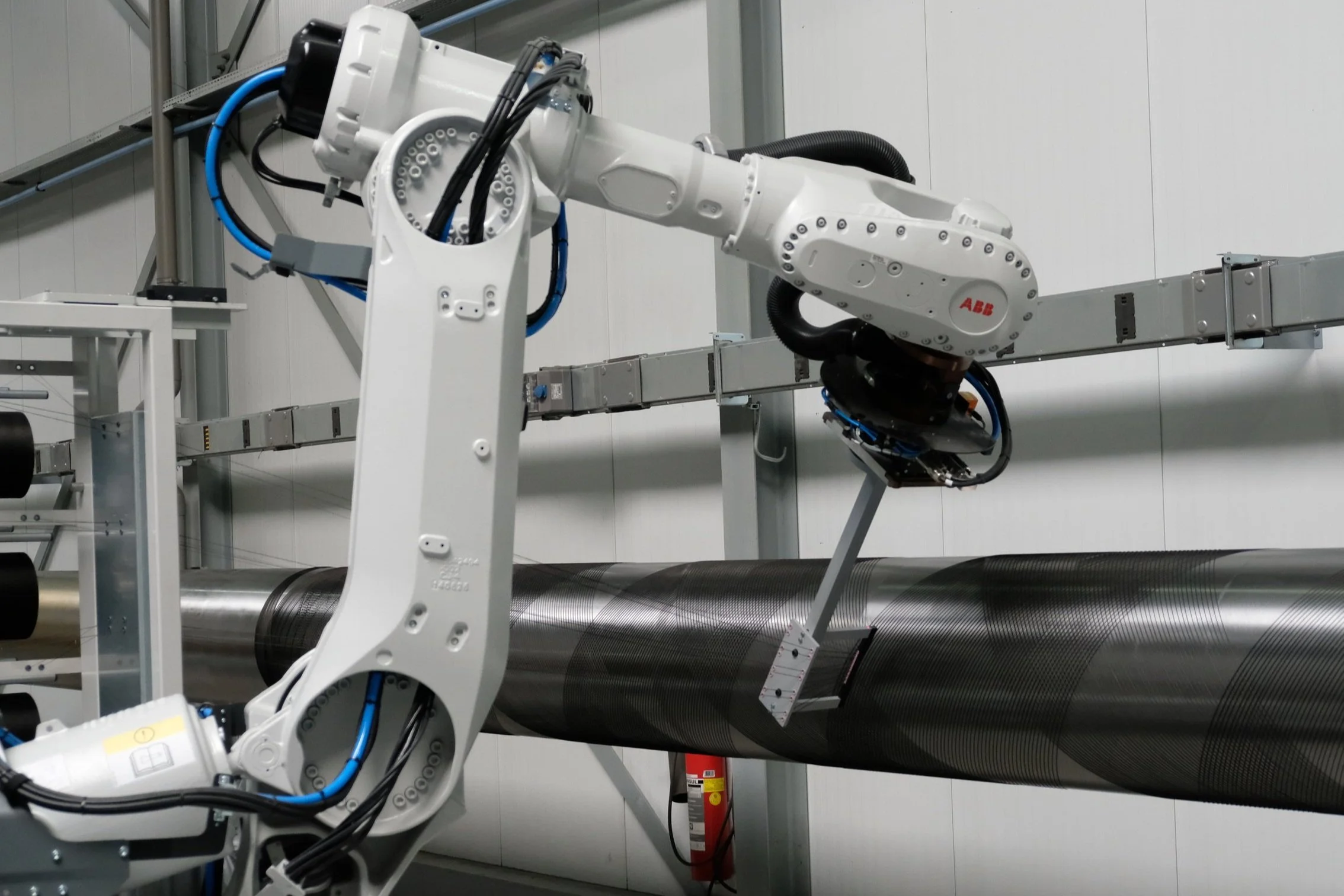
Robot Arm
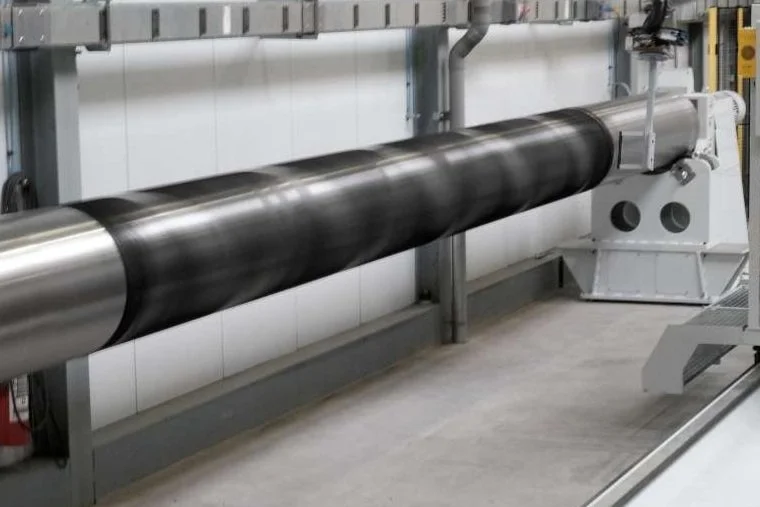
External Axis/Mandrel
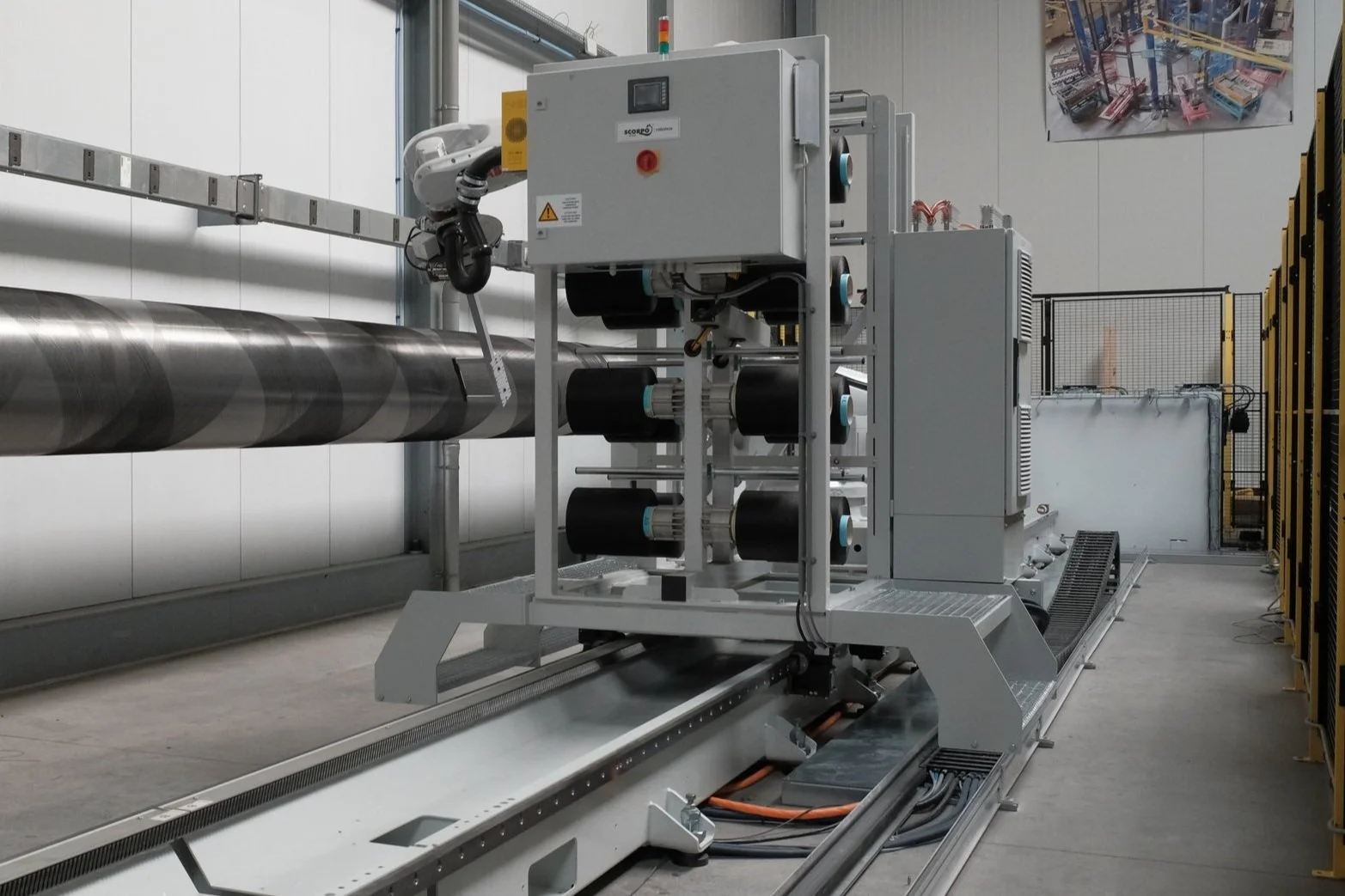
Pedestal/Track
Scorpo Gemini
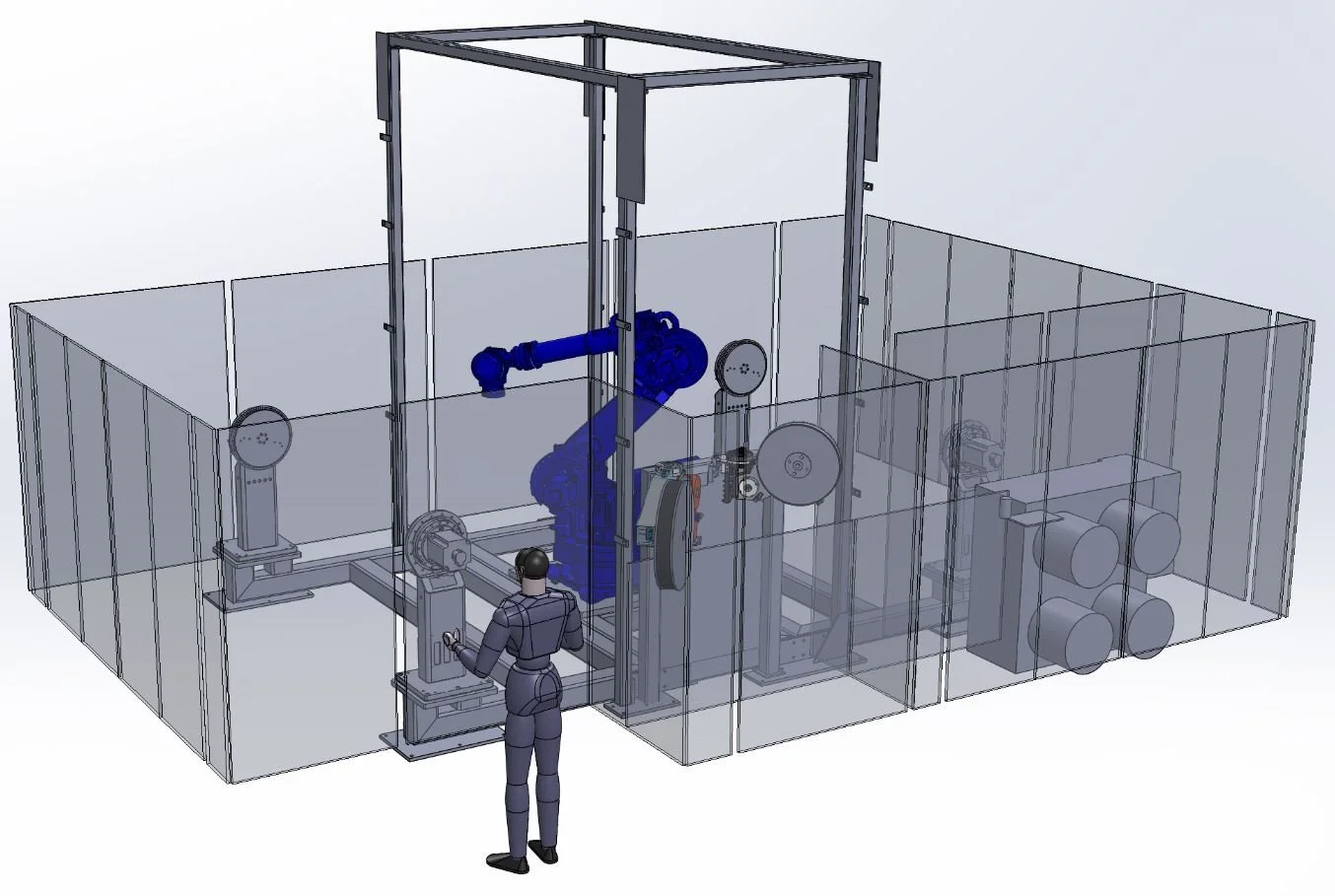
Rendering Overview

Robot Arm
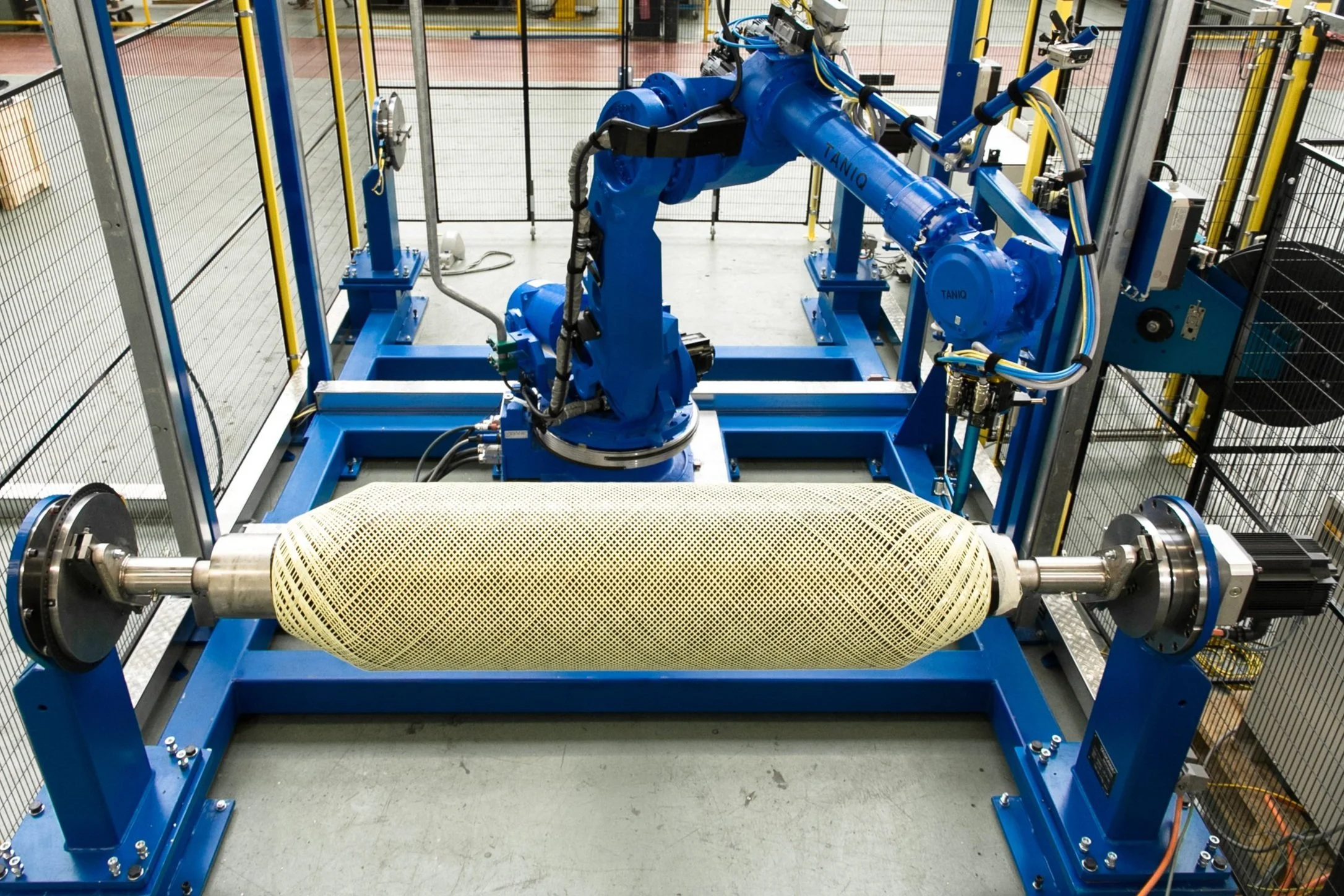
External Axis/Mandrel
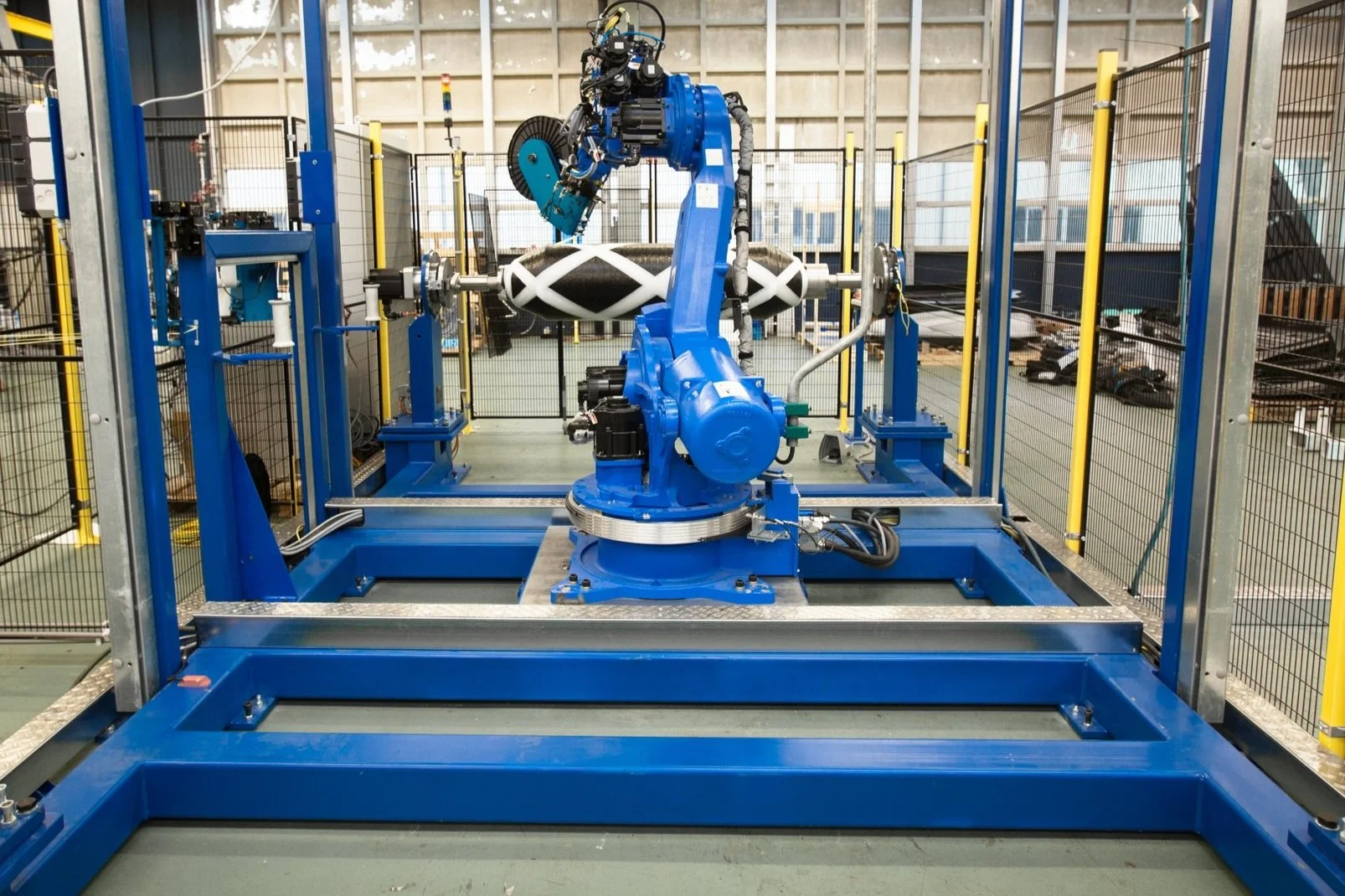
Pedestal
